08.12.20 – Additive Manufacturing In-Situ Resources Utilization (AMISRU) is a research project led by the Thermomechanical Metallurgy Laboratory (LMTM) and supported by the EPFL Space Center (eSpace) and has been recently funded by the European Space Agency and the Swiss Space Office of the State Secretariat for Education, Research and Innovation (SERI) for two years. That’s the perfect time to have a closer look at a program that combines the utilization of lunar regolith as a feedstock and state-of-the-art laser beam and its expected goals: to produce both oxygen and metal to sustain human life and manufacture complex objects on the Moon. And beyond.
Building on the Moon
Furthermore, the incorporation of Additive Manufacturing (AM) into ISRU allows us to progress beyond the supply of consumables to the construction of complex objects using processed materials and layered construction. The products of the lunar ecology constitute feedstock for AM which provides a general-purpose manufacturing technique without the waste inherent to the more traditional subtractive techniques.
Based on the analysis of various Luna and Apollo samples, it is known that oxygen is the most abundant element in the lunar regolith, accounting for 40-45% by mass. However, this oxygen is chemically bound in the regolith material as oxides, in the form of minerals, and it is unavailable for immediate use. Other chemical and mineral resources such as metals are considered as valuable resources, particularly as they often are produced as by-products of extraction processes. Accordingly, after the oxygen extraction from the lunar regolith, a mixture of metallic and metalloid elements (e.g. Al, Ti, Fe, Mg, Ca, Na and Si) is left behind which could be utilized for the fabrication of the required structural parts on the lunar surface (and other planetary bodies).
Lasers and algorithms
AMISRU project is funded bilaterally by the European Space Agency (ESA) – Open Space Innovation Platform (OSIP) and the Swiss Space Office of the State Secretariat for Education, Research and Innovation (SERI/SSO) – Mesure du Positionnement (MdP2020) for two years of study taking place jointly at Thermomechanical Metallurgy Laboratory (LMTM) and the EPFL Space Center (eSpace). The study focuses on the deep dive investigation of the laser-material (ISRU metallic by-product) interaction in terms of the governing thermo-mechanical and fluid-dynamical phenomena. The study employs an in-house Laser Powder Bed Fusion (LPBF) system incorporated with state-of-art laser beam manipulating module and in-situ observation technologies to acquire the maximal control over the laser-material interaction zone. Moreover, instead of conventional process optimization methods which require extensive amounts of trials and error, the project employs numerical analysis via Finite Element Method (FEM) and machine learning algorithms to minimize the required resources.
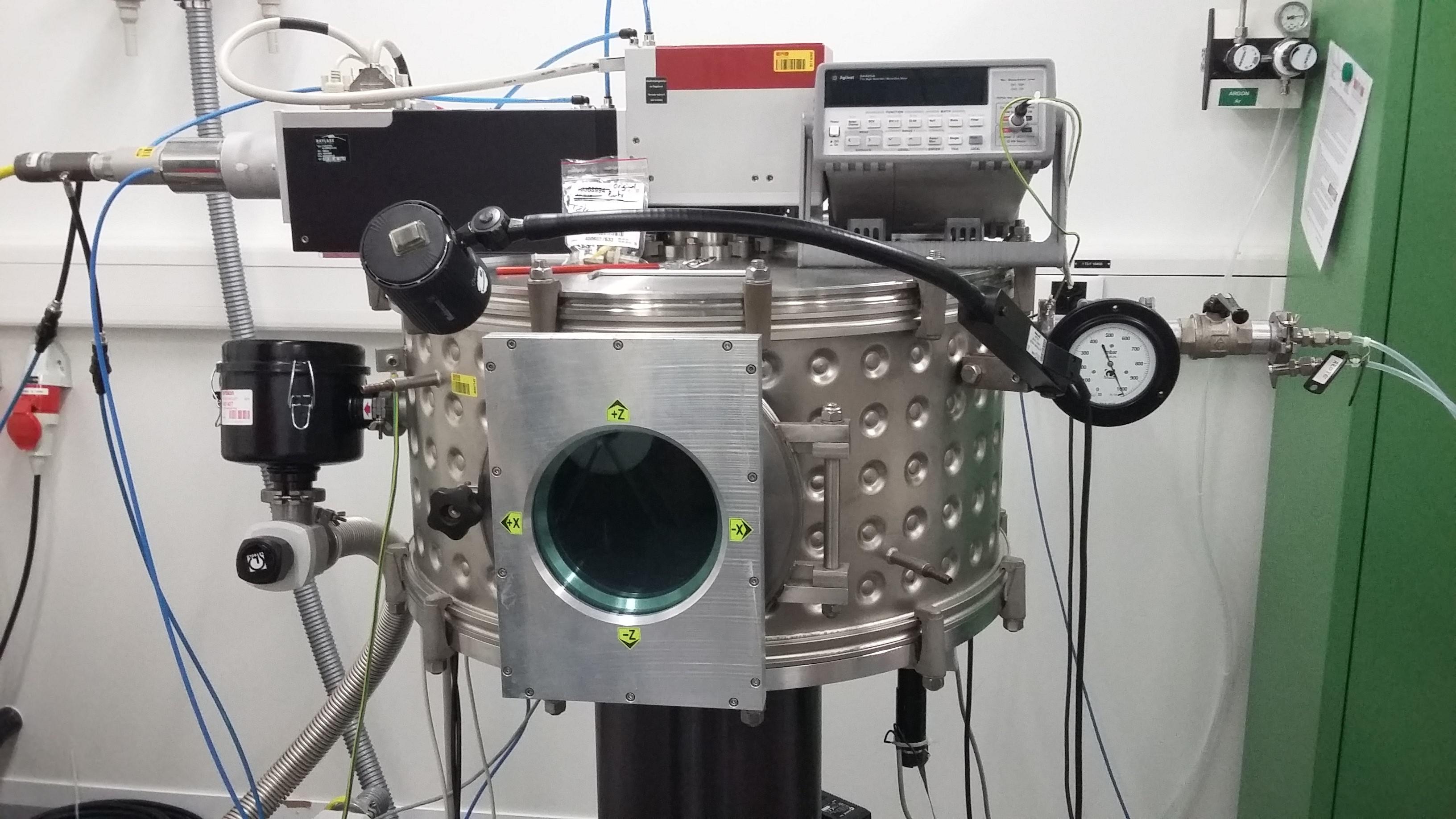
In-house Laser Powder Bed Fusion (LPBF) system at LMTM EPFL
Laser processing of the ISRU metallic by-product could be dominantly challenging compared to the materials employed for LPBF to this date. This is due to the heterogenous chemical composition of these materials, high quantities of low vapor pressure elements such as Mg, Ca, Na and remaining oxygen from the extraction process. These perks could result in extensive melt pool instabilities and generation of a consolidated material with unsuitable levels of porosity and dimensional accuracy. In addition, these feedstocks possess irregular powder geometries which could inhibit the flowability and spreadability of the feedstock on the powder bed; an added value to the complexity of the process.
Consequently, having maximum control on the process can significantly reduce the corresponding process challenges of ISRU metallic by-products. The project will pay specific attention to the printability of ISRU material and discovering ways to improve the process which will be followed up by full material and mechanical characterization methods to confirm the applicability of such material and process for the corresponding atmosphere and applications.
A first interplanetary step
AMISRU is part of a much larger roadmap which might extent to the next 10 years covering a number of potential processing technologies, design of novel metallic alloy systems based on the present elements on the planetary bodies of interest, etc.
Funding
European Space Agency (ESA) – Open Space Innovation Platform (OSIP)
Swiss Space Office (SSO) – Mesure de Positionnement (MdP2020)